Making the right choice in conveyor systems can significantly influence your business’s efficiency, safety, and bottom line. The right system will seamlessly integrate into your existing operations, minimizing disruptions and maximizing productivity. This guide will help you navigate through the critical considerations to make an informed decision that suits your specific needs.



Understanding Your Needs
Volume of Goods: Tailoring Capacity to Demand
The volume of goods you handle daily sets the stage for the type of conveyor system that will best serve your operations. Are you dealing with a high throughput of goods, or is your operation more modest in scale? Heavy-duty systems are designed to tackle large volumes, while their lighter counterparts are better suited for smaller quantities.
Nature of the Product: Matching Conveyors to Merchandise
No two products are the same, and neither should be the conveyors that handle them. Consider the size, weight, and condition of your merchandise. Delicate or smaller items find their ally in belt conveyors, while chain conveyors step up to the plate for heavy, hot, or bulky goods.



Analyzing Your Space
Available Space: Maximizing Efficiency Within Constraints
Space constraints are a reality for many businesses. It’s imperative to assess the available area within your facility. If floor space is at a premium, overhead conveyors provide an elegant solution. On the other hand, roller or belt conveyors shine in larger spaces, ensuring goods move efficiently from point A to B.
Layout Considerations: Navigating Turns and Direct Paths
The layout of your facility is like the blueprint of a well-choreographed dance. Curved conveyors gracefully navigate turns, making them ideal for facilities with a multitude of twists and turns. Meanwhile, straight conveyors offer a more direct path, ensuring a seamless flow from one end to the other.
Considering Your Budget
Initial Costs: The Starting Line of Investment
Budget considerations are pivotal in any decision-making process. Initial costs encompass the purchase price of the conveyor system and the expense of installation. It’s the starting line of your investment journey.
Operational Costs: Balancing the Scales
Looking beyond the initial outlay, it’s essential to factor in operational costs. This includes energy consumption, maintenance, repairs, and the potential for downtime. While more efficient systems may command a higher initial cost, they often prove to be more economical in the long run.



Evaluating Additional Features
Automation Needs: Streamlining Operations for Efficiency
Automation can be a game-changer in optimizing your operations. Automated conveyor systems have the potential to significantly reduce labor costs while enhancing overall efficiency. However, it’s important to note that they may require a larger initial investment.
Safety Features: Prioritizing Workplace Safety
Safety should always be at the forefront of any industrial operation. Consider conveyor systems equipped with features like emergency stop buttons and safety guards. These additions act as a safeguard, preventing accidents and ensuring the well-being of your workforce.
Future-proofing: Investing in Longevity
Businesses evolve and grow. Choosing a conveyor system that can easily adapt to these changes is a strategic move. Look for systems that can be expanded or upgraded, ensuring your investment stands the test of time.



FAQs: Navigating Common Queries
Q1: Can I retrofit my existing conveyor system to meet changing needs?
A1: Yes, many conveyor systems can be modified or upgraded to accommodate evolving requirements. Consulting with a professional provider can help determine the best approach for your specific situation.
Q2: What safety measures should I prioritize for my conveyor system?
A2: Essential safety features include emergency stop buttons, safety guards, and regular maintenance checks. Training your staff on proper usage and safety protocols is equally crucial.
Q3: How do I calculate the ideal conveyor speed for my operations?
A3: Conveyor speed is influenced by factors such as the type of product, desired throughput, and the layout of your facility. Consulting with an expert can help pinpoint the optimal speed for your specific needs.
Q4: Are there eco-friendly options for conveyor systems?
A4: Yes, there are eco-conscious conveyor systems designed with energy efficiency and sustainability in mind. These options can not only reduce environmental impact but also lead to cost savings in the long run.
Q5: Can I integrate automation into my existing conveyor system?
A5: In many cases, existing conveyor systems can be retrofitted with automation components. However, it’s crucial to work with a knowledgeable provider to ensure seamless integration and optimal performance.
Q6: What is the typical lifespan of a conveyor system?
A6: The lifespan of a conveyor system varies depending on factors like usage, maintenance, and environmental conditions. Well-maintained systems can last anywhere from 10 to 20 years or more.

Conclusion: Investing in Your Business’s Future
Selecting the right conveyor system is more than a business decision—it’s an investment in the future of your company. By carefully considering your specific needs, space constraints, budget, and additional requirements, you’re positioning your business for enhanced efficiency, safety, and profitability. Seek guidance from professional conveyor system providers who can offer invaluable insights and guide you through the selection process. Remember, a well-chosen conveyor system is a cornerstone of a thriving operation.
Types of Conveyor Systems and Their Applications in Different Industries
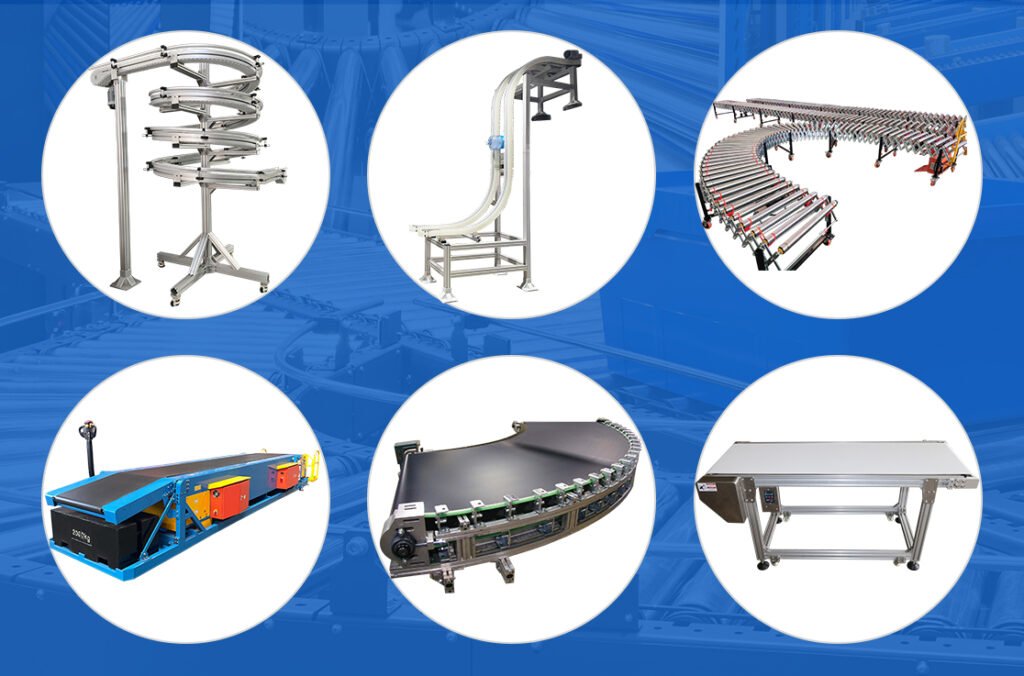